Behind the science of GSK
Innovation stories from GSK
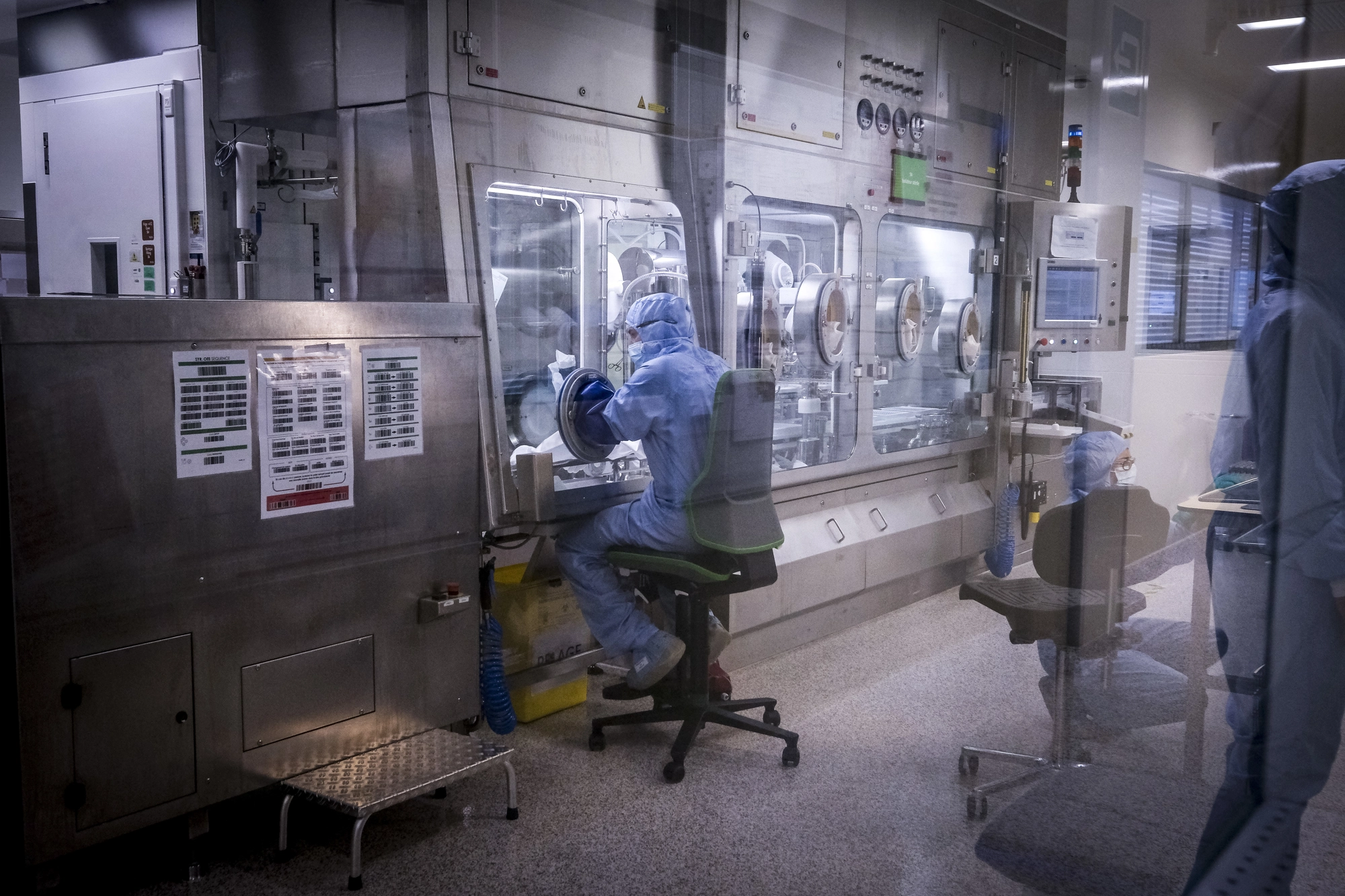
Behind the science of GSK
Innovation stories from GSK
Feature
‘It’s insidious and it’s getting worse’: AMR and the urgent need for novel antibiotics
5 min read time
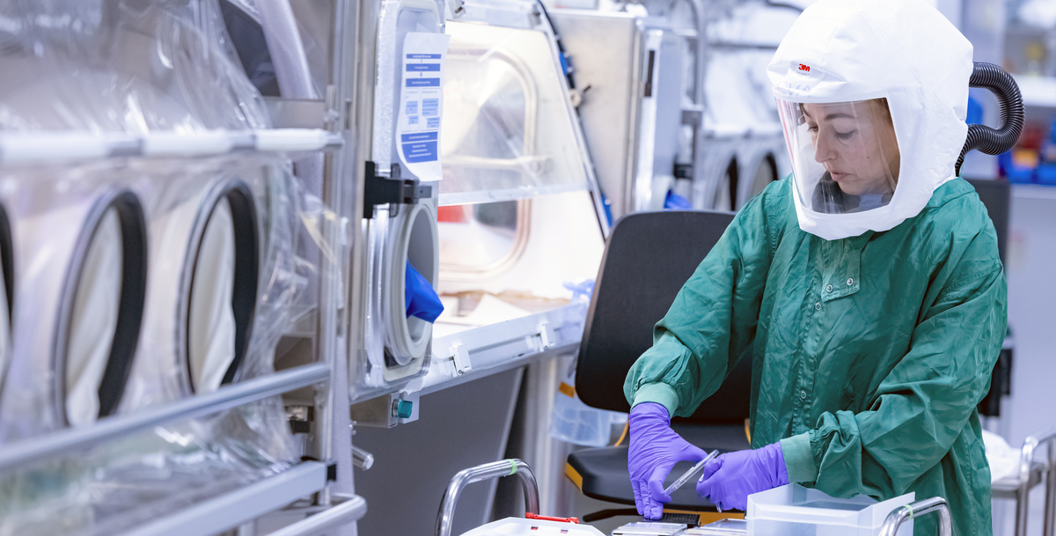
Feature
Scientists gain ground in centuries-long malaria struggle – but more innovation is needed to stay ahead of evolving parasites
6 min read time
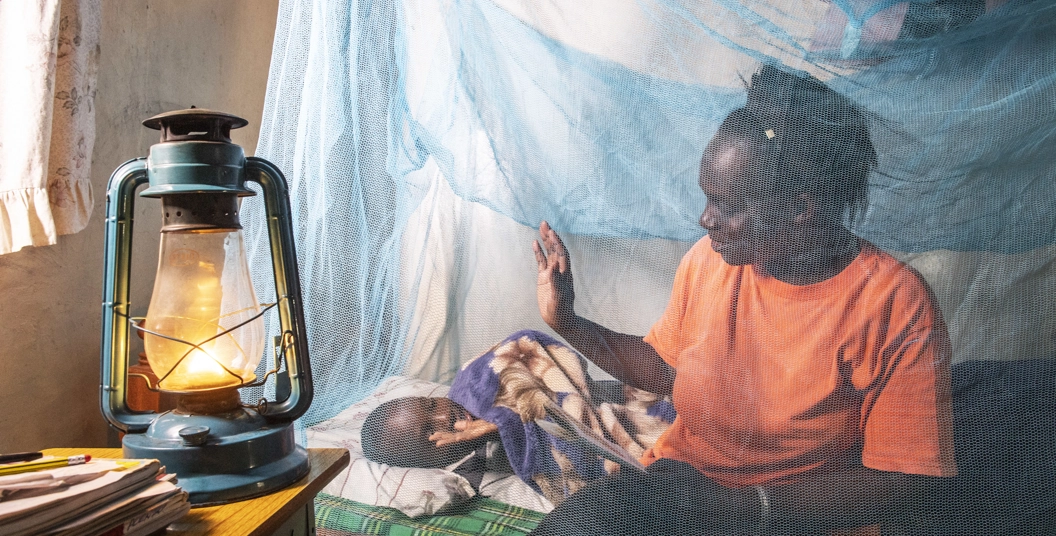
Feature
Robots, AI, and machine learning: how smart manufacturing is getting medicines and vaccines from factories to patients faster
4 min read time
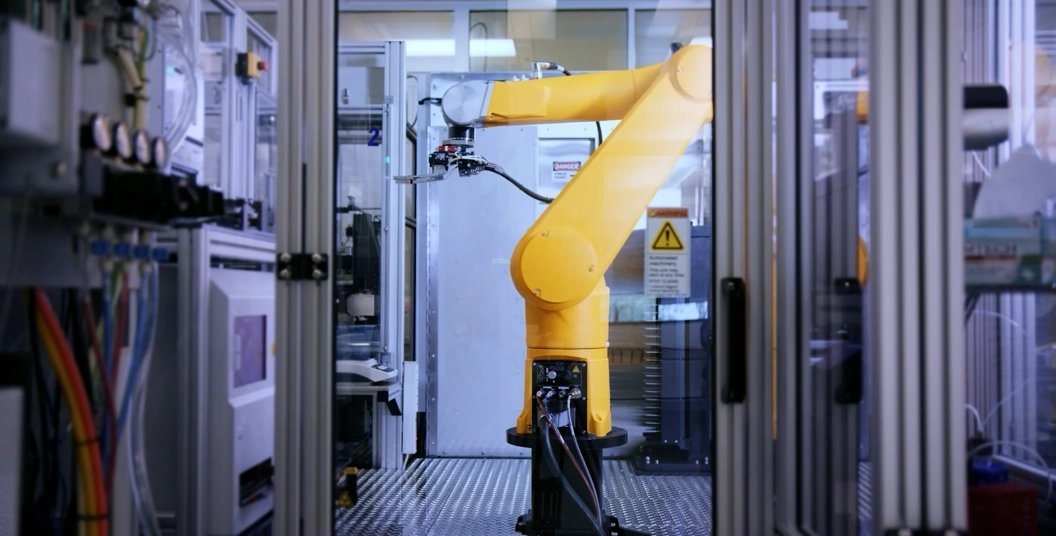
Feature
‘Patients can breathe easier today’: Scientific advances in asthma and COPD care could prevent irreversible lung damage
5 min read time
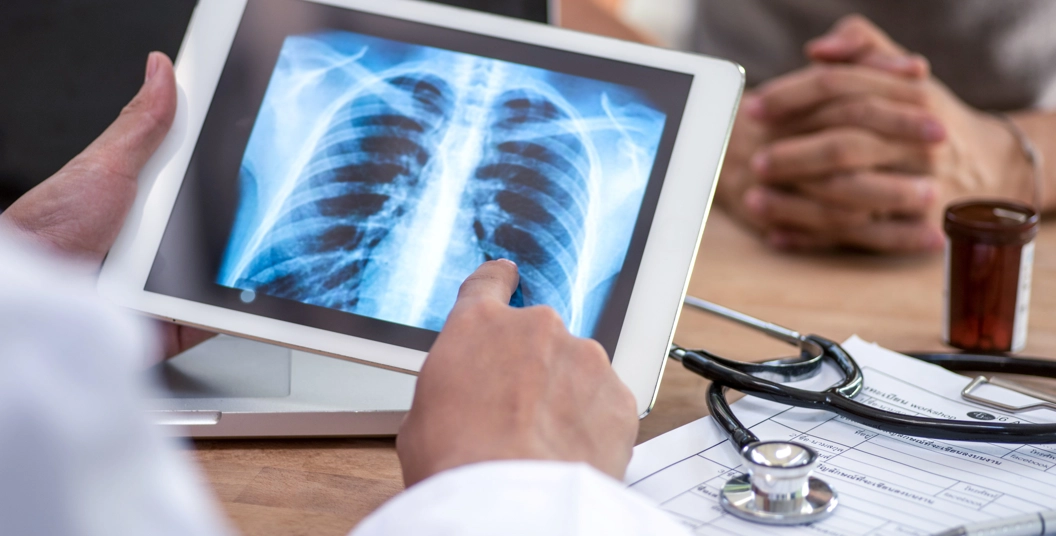
Feature
‘It is both a strategic and a moral imperative’: Why closing the health equity gap is better for everyone
5 min read time
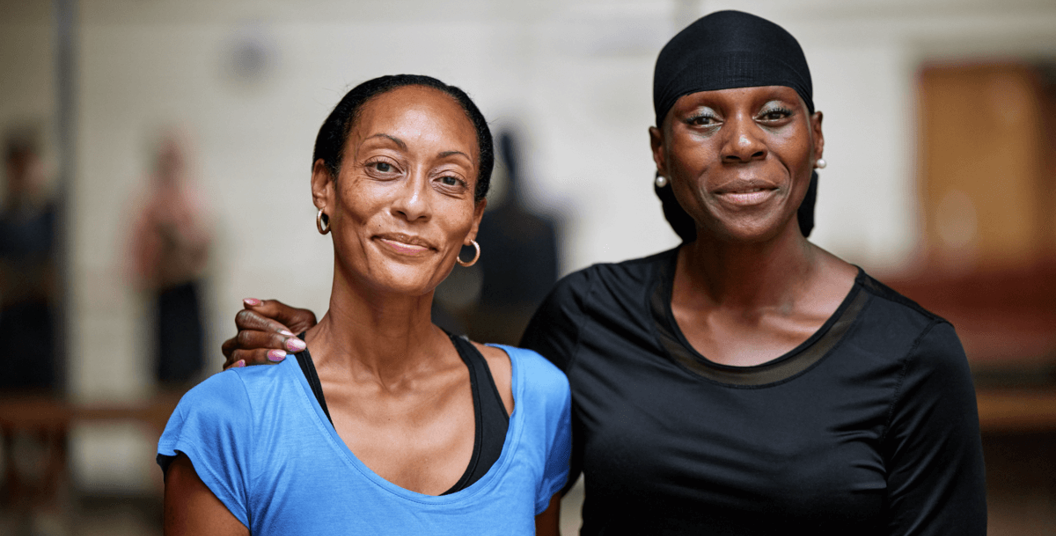
Opinion
'Prevention is the best medicine to stop disease before it starts'
By GSK Team - 3 min read time
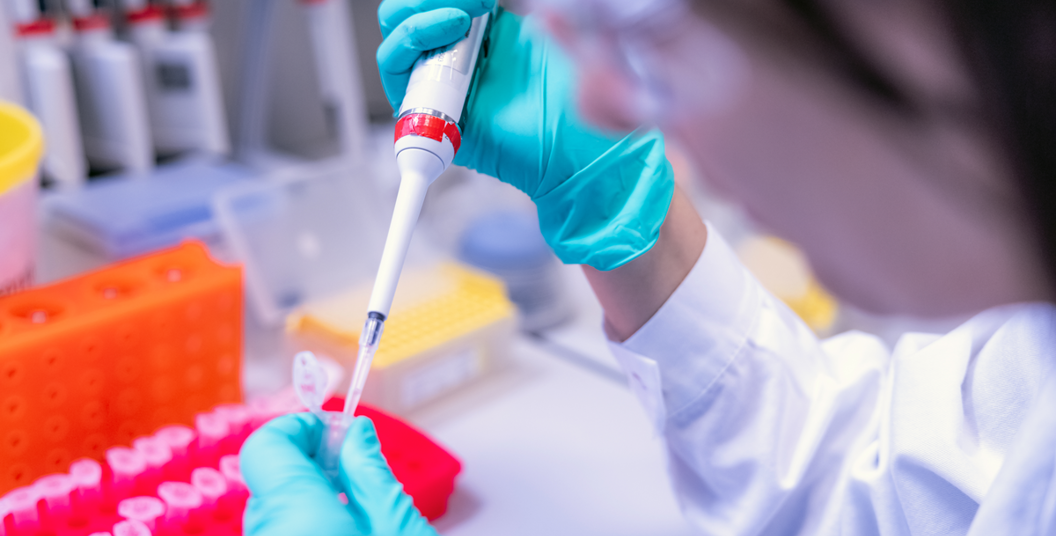
Feature
‘It’s insidious and it’s getting worse’: AMR and the urgent need for novel antibiotics
5 min read time
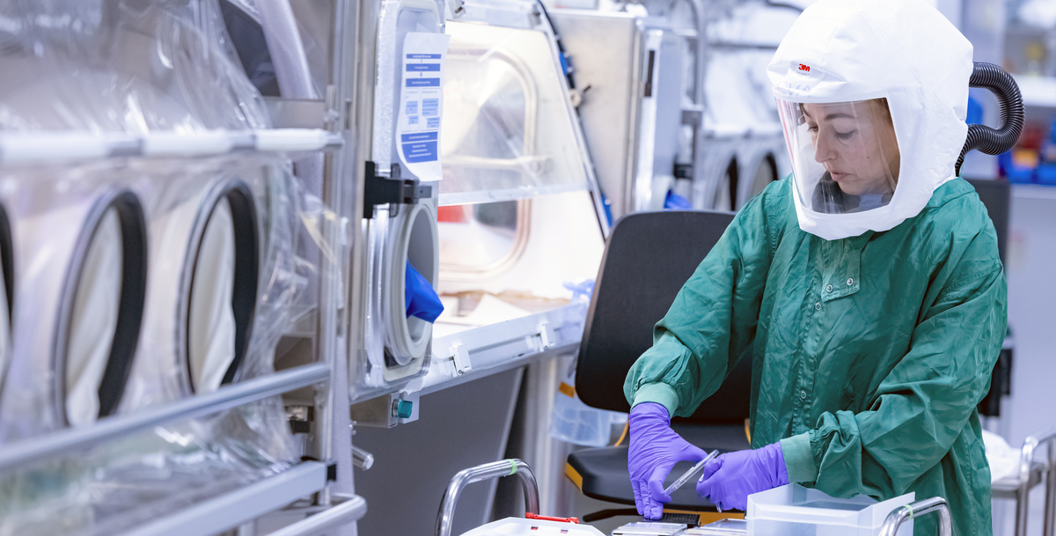
Feature
Scientists gain ground in centuries-long malaria struggle – but more innovation is needed to stay ahead of evolving parasites
6 min read time
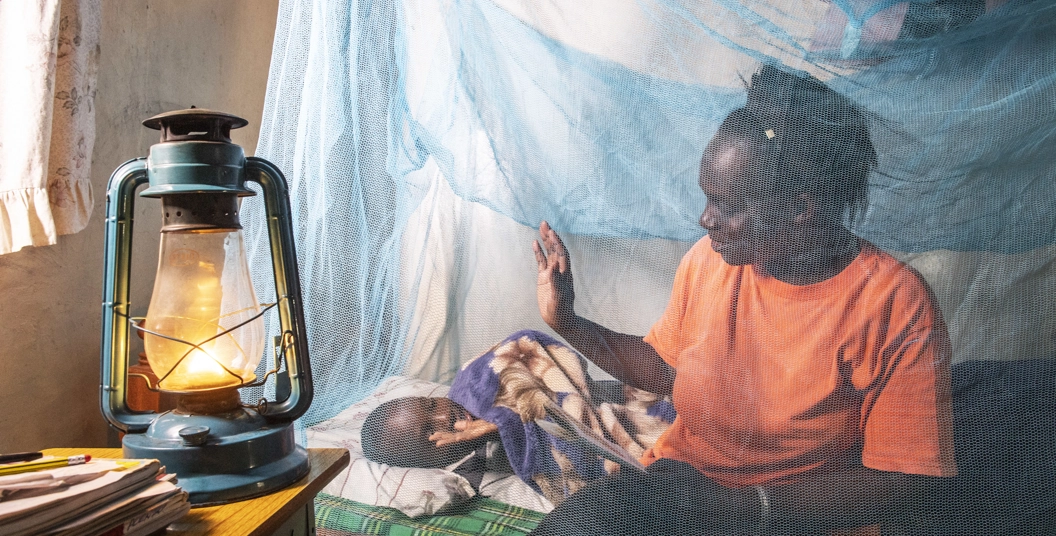
Feature
Robots, AI, and machine learning: how smart manufacturing is getting medicines and vaccines from factories to patients faster
4 min read time
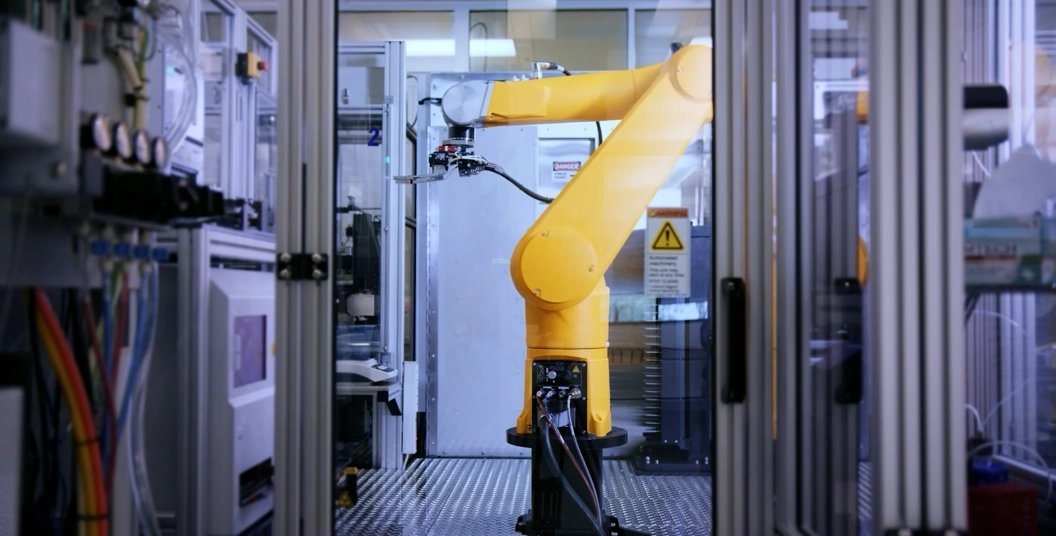
Feature
‘Patients can breathe easier today’: Scientific advances in asthma and COPD care could prevent irreversible lung damage
5 min read time
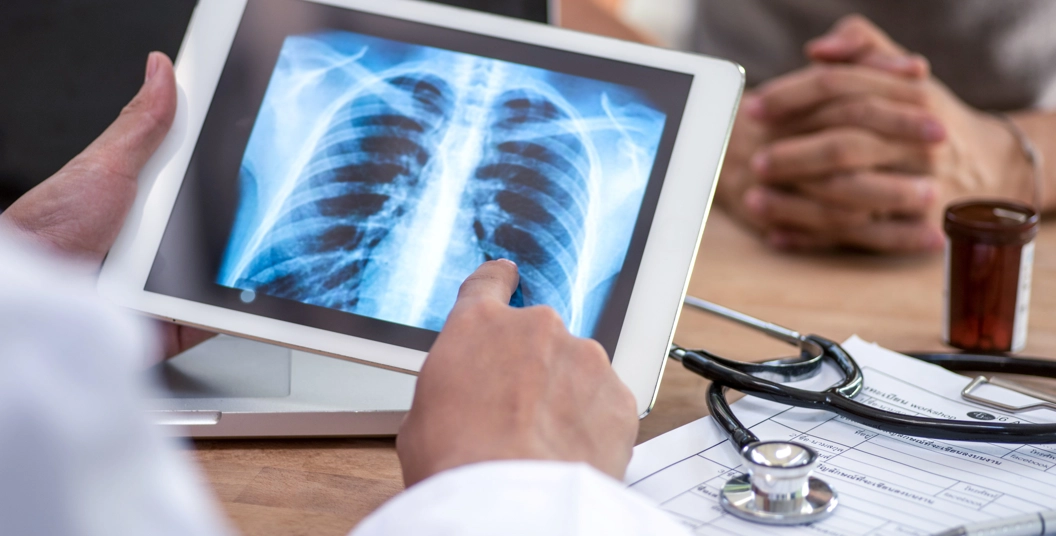
Feature
‘It is both a strategic and a moral imperative’: Why closing the health equity gap is better for everyone
5 min read time
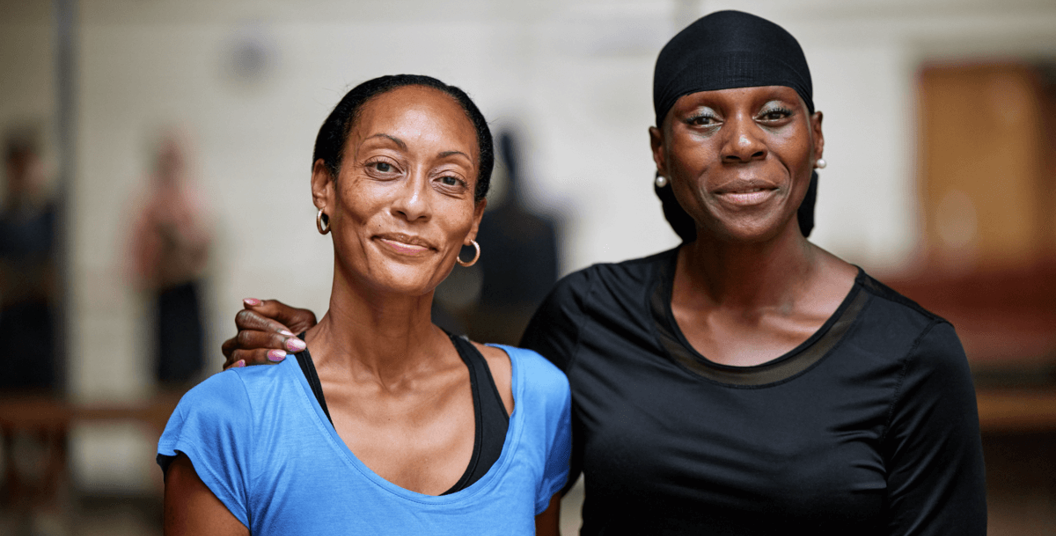
Opinion
'Prevention is the best medicine to stop disease before it starts'
By GSK Team - 3 min read time
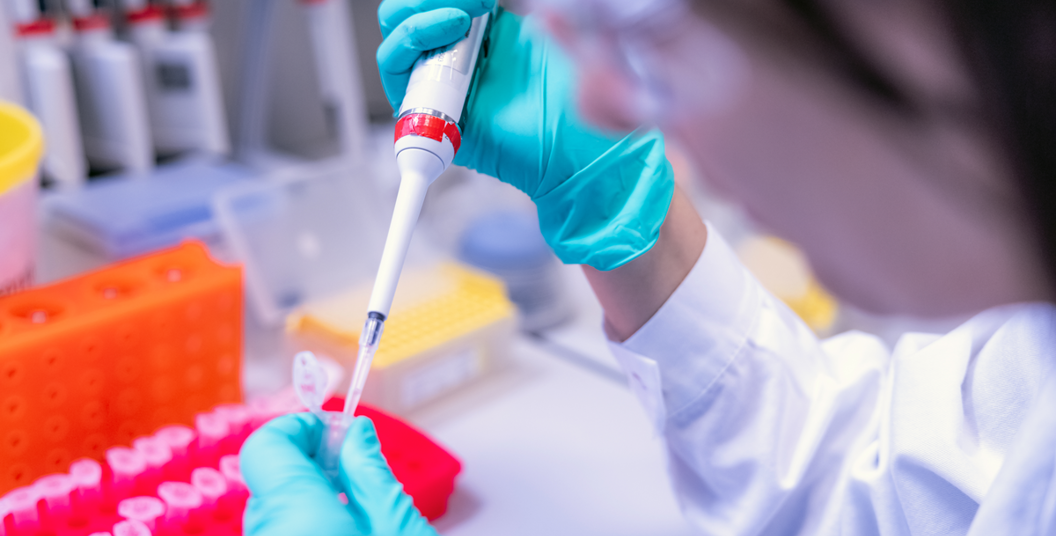
Innovation videos
0:37
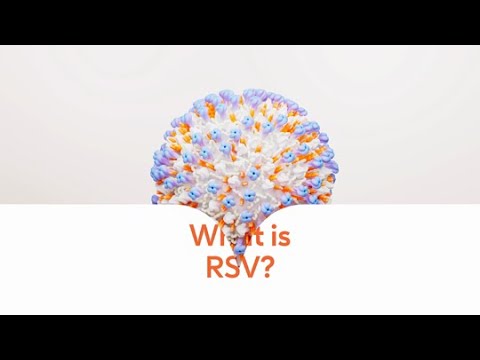
Science explainer
What is RSV?