Global supply chain
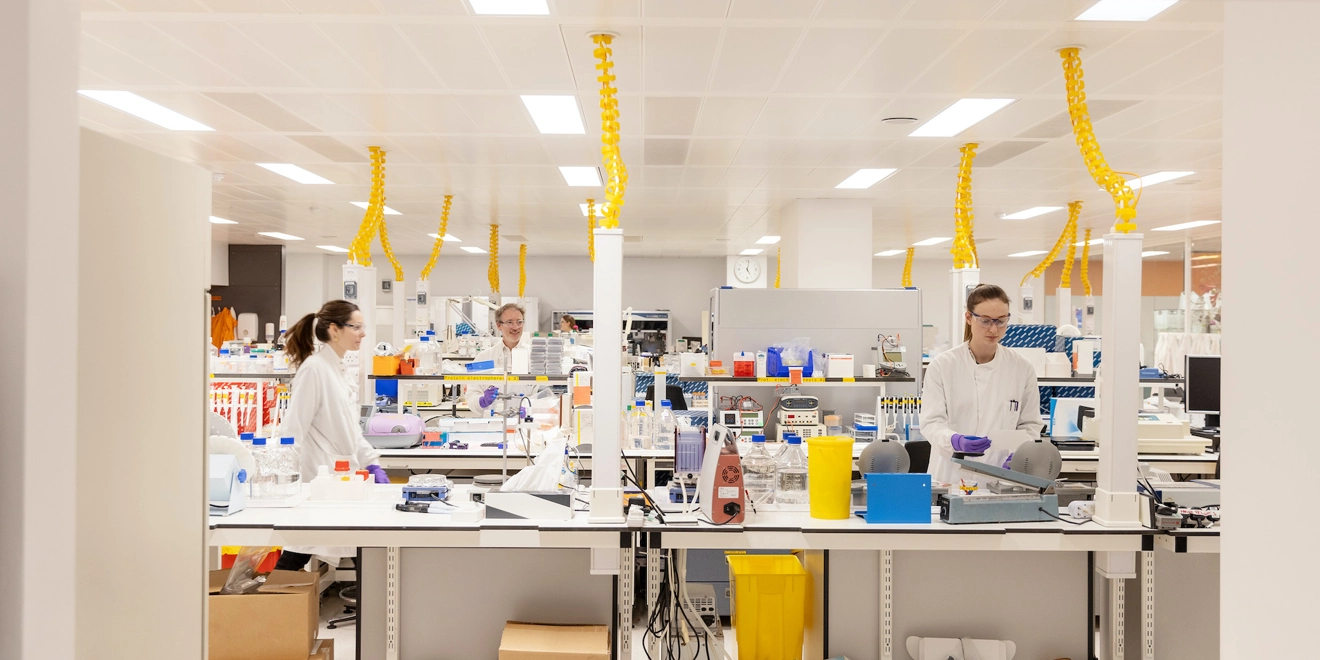
Our global supply chain is critical to manufacturing and supplying reliable, high-quality medicines and vaccines to meet patients’ needs and drive our performance. It includes 37 medicines and vaccines manufacturing sites which help to make a positive impact on the health of millions of people.
It is vital for innovation too. Supply chain teams are part of how we prevent and change the course of disease, bringing our innovations to patients as quickly, efficiently and effectively as possible. They’re involved early in product and process development, working with R&D to make sure that what works in clinical trials can be scaled up to commercial production.
Technology is transforming how we manufacture medicines and vaccines, enabling us to increase the speed, quality and scale of product supply. We’re using data to help us monitor production in real time, spot ways to increase yields and predict when equipment needs maintenance. We’re using smart manufacturing technologies for greater efficiency, productivity, sustainability and cost savings. We can augment our human creativity, expertise and problem solving with data and AI, increasing our impact and delivering better and faster for patients.