Outstanding people
Uniting science, technology and talent to get ahead of disease together.
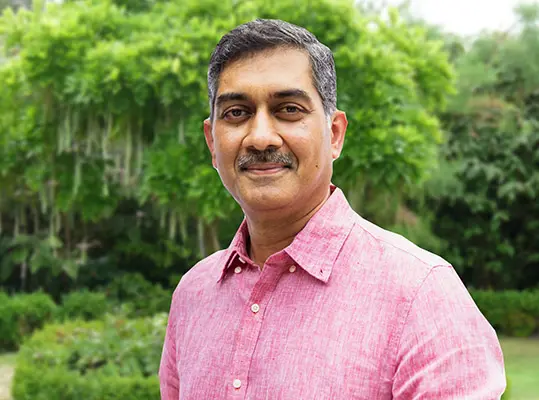
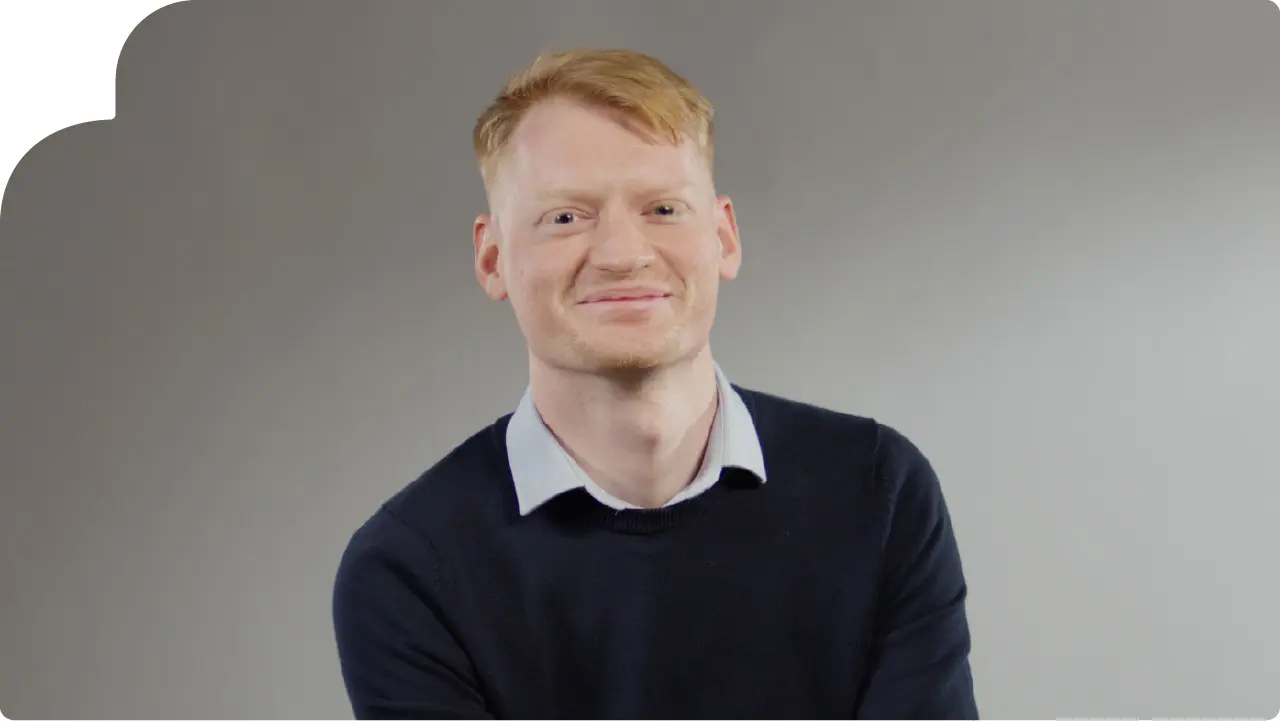
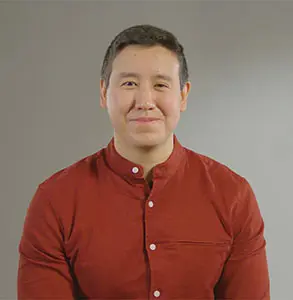
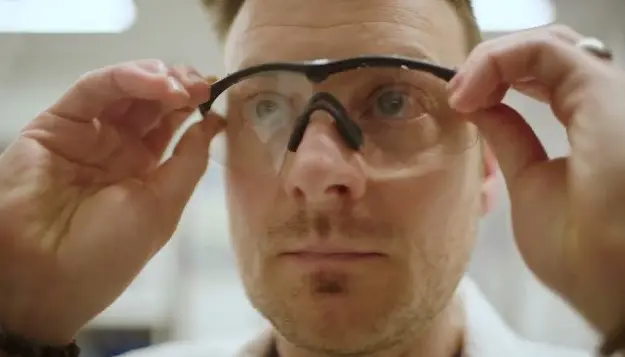
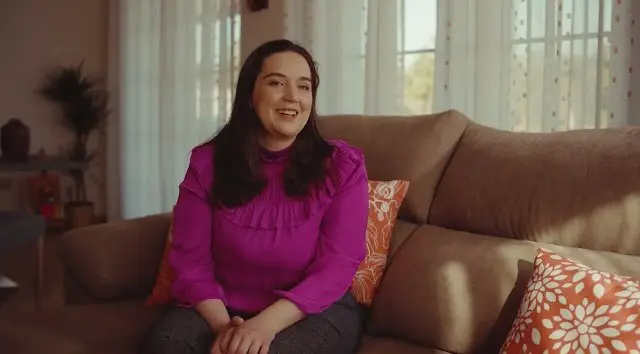
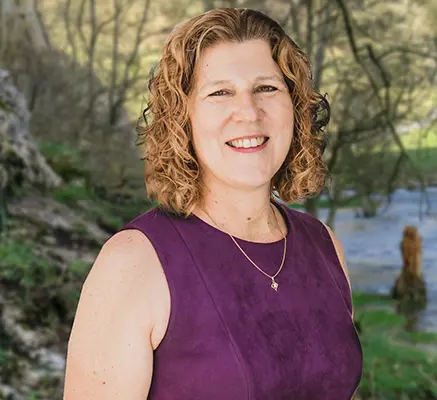
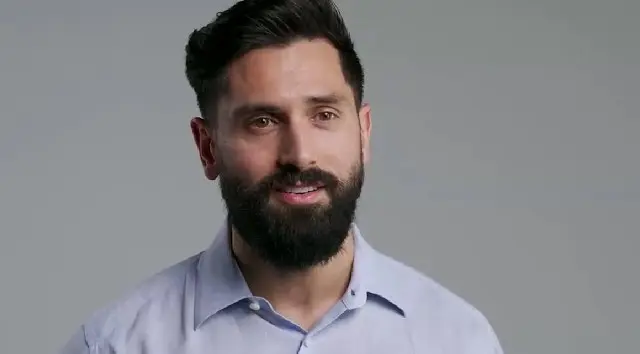
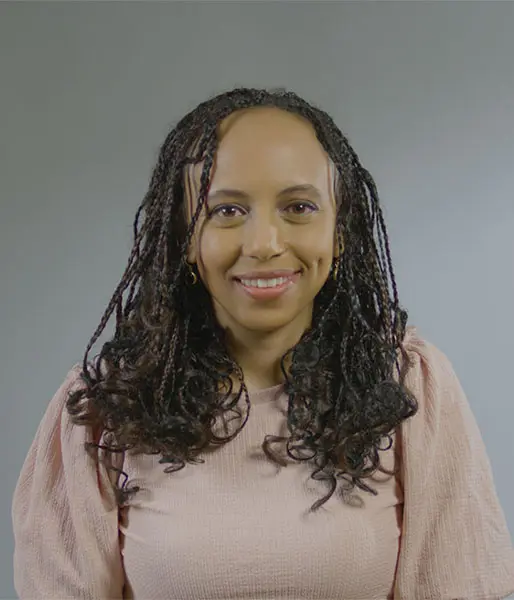
Must watch videos (10 videos)
Scroll to explore
Browse our series
Great place to work (8 videos)
Meet some of the people who make GSK a great place to work.
View series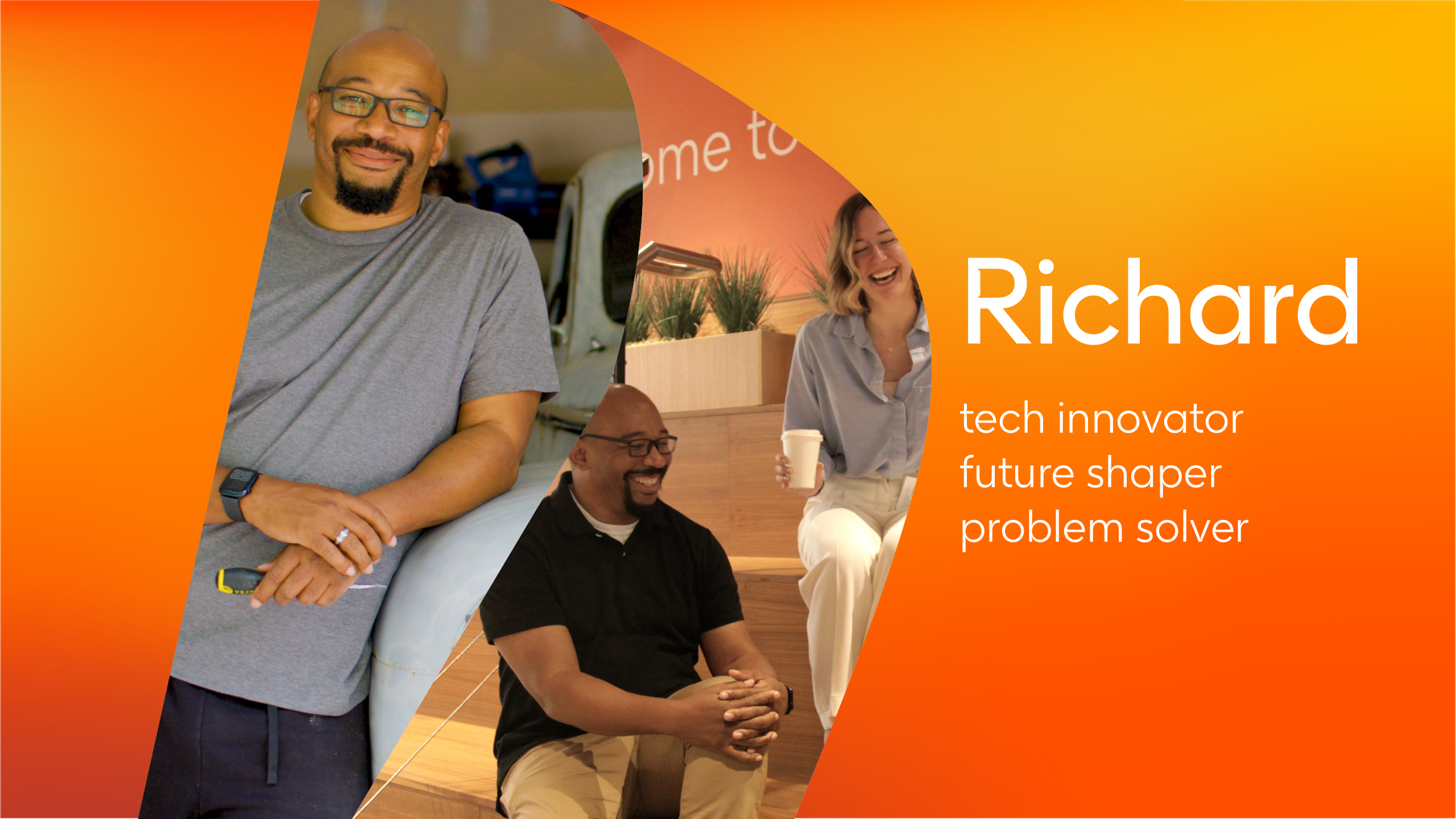
Latest episode
Meet Richard: tech innovator, future shaper, problem solver, helping us to accelerate our pipeline and performance using advanced technologies.
Meet our veterans (4 videos)
Our Veterans bring immense value to GSK and we have a strong commitment to support and mentor service personnel and civil service members as they transition into the corporate environment.
View series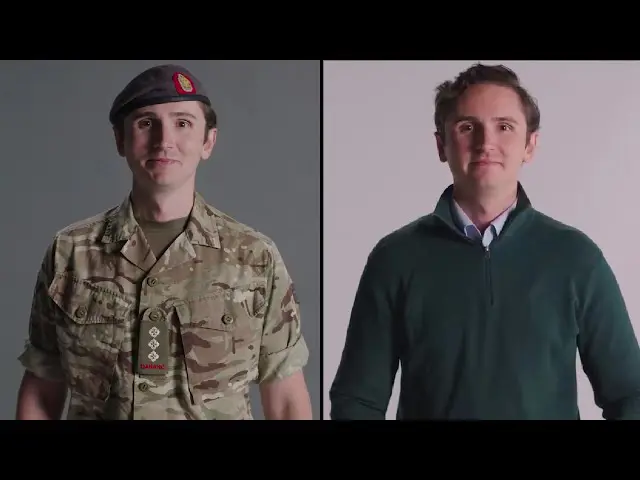
Latest episode
Veterans at GSK
Working together (5 videos)
From inclusion and diversity to sustainability and global health, discover how our people are using their interests and passions to help us get ahead together.
View series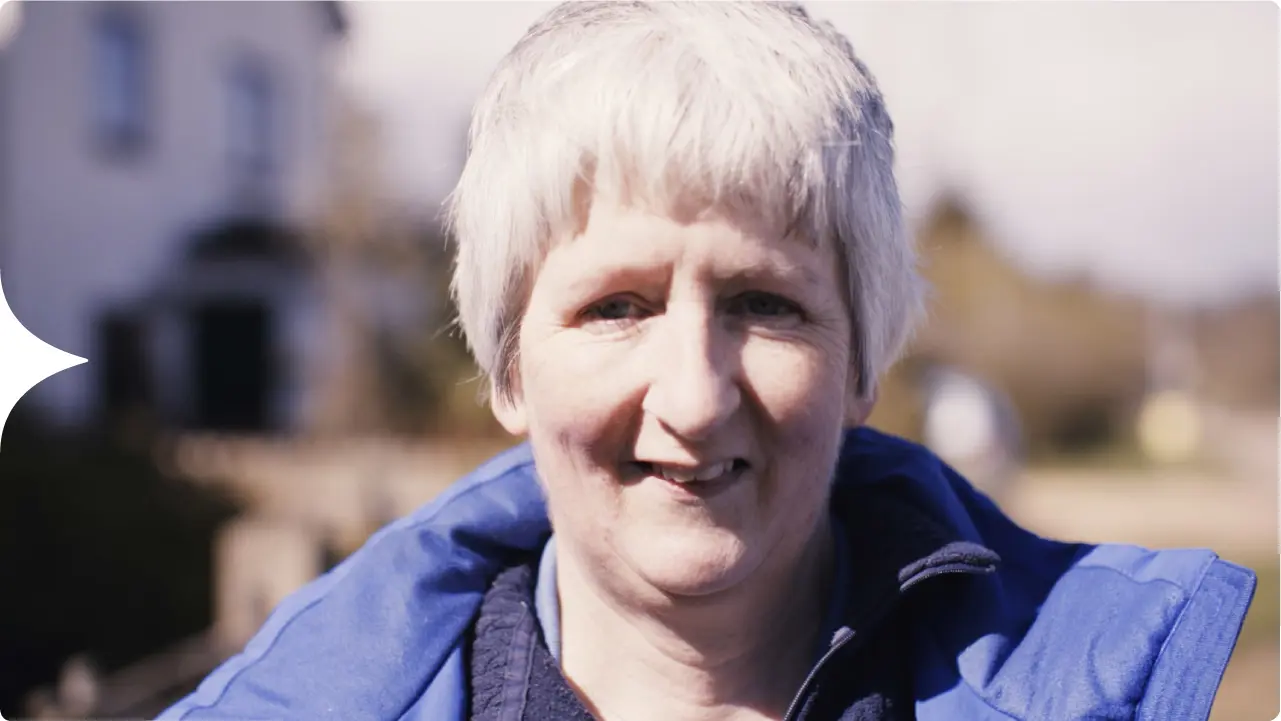
Latest episode
Meet Fiona: improving health and wellbeing through nature
My GSK story (8 videos)
Find out more about the people behind our work, the contribution they make to GSK each day and how they’re embracing our culture.
View series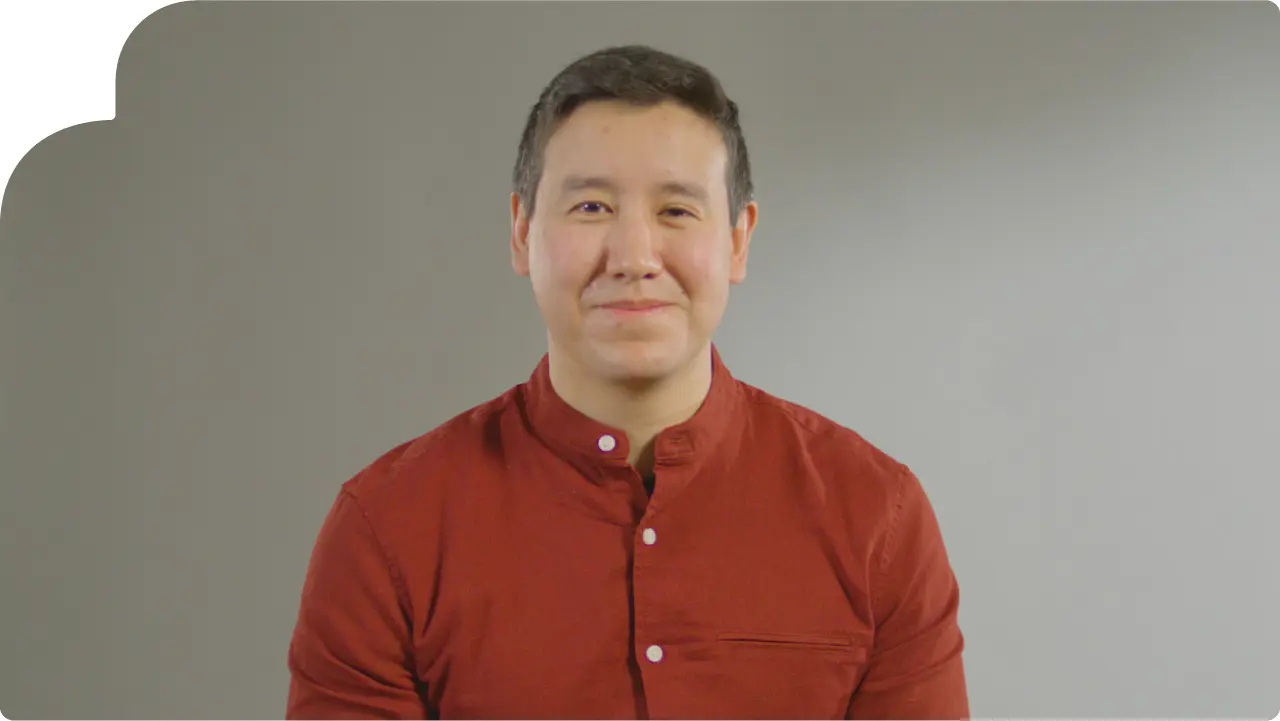
Latest episode
Meet Dominic: being ambitious for patients
Innovating together (11 videos)
Learn how our people are using the science of the immune system, human genetics and advanced technologies to find new treatments for patients.
View series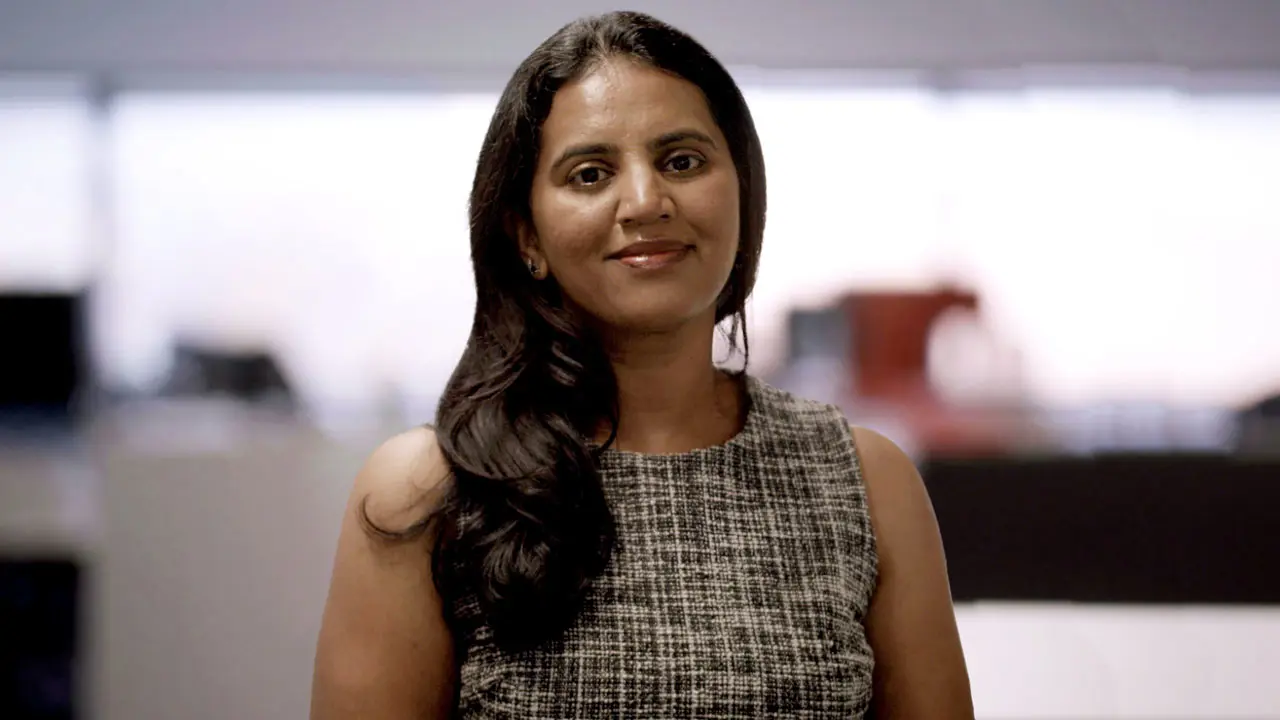
Latest episode
Meet Mugdha: working together to help more patients